Mirrors: How to Choose the Right Solution
May 23, 2025
Mirrors: Effective supervision and risk management are vital for any modern business. Observation solutions—such as industrial, food-grade, and security viewing devices—play a crucial role in boosting safety, productivity, and operational efficiency. Whether you operate a warehouse, a food processing unit, or a retail environment, selecting the appropriate product ensures the smooth running of your enterprise.
Total Locker Service offers a comprehensive range of observation tools tailored for diverse environments. This guide walks you through the key considerations for selecting the best option for your specific needs, covering application areas, materials, installation tips, and unique features for different industries.
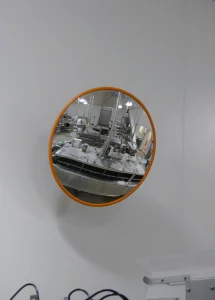
Mirrors Understanding the Need for Enhanced Visibility
Every workplace faces unique challenges regarding visibility and surveillance. Blind spots, busy corridors, and high-traffic zones increase the risk of accidents or security breaches. Enhanced visibility is not just about safety; it supports better workflow management, theft deterrence, and regulatory compliance.
By investing in specialised viewing solutions, businesses create safer, more efficient spaces. Whether you need to observe production lines, monitor loading bays, or deter unauthorised activity, the right product makes a measurable difference.
Industrial Environments: Durability and Safety
Manufacturing sites and distribution centres are often vast and complex. The sheer scale can lead to areas that are hard to monitor. In these settings, the right observation tool helps supervisors oversee workflow, prevent collisions, and comply with health and safety standards.
Key Features for Industrial Use:
- Robust Construction: Solutions must withstand impacts, dust, and temperature changes. Materials like polycarbonate or stainless steel are commonly used due to their strength and longevity.
- Wide Viewing Angles: Larger models provide a panoramic view of factory floors, intersections, or storage aisles.
- Easy Mounting: Adjustable brackets and flexible mounting systems facilitate installation at entrances, intersections, or machinery zones.
Total Locker Service offers a range specifically designed for harsh environments. Their heavy-duty models resist shattering and are easy to clean, making them ideal for demanding industrial applications.
Mirrors Food Industry: Hygiene and Compliance
Processing plants and kitchens have unique requirements. Hygiene and compliance with food safety regulations are paramount. Equipment in these spaces must resist moisture, chemicals, and frequent cleaning.
Choosing for Food Environments:
- Non-Toxic Materials: Food-grade plastics and stainless steel eliminate the risk of contamination.
- Seamless Edges: Smooth surfaces prevent debris buildup and make sanitation easy.
- Condensation Resistance: Special coatings minimise fogging in high-humidity or chilled environments.
Total Locker Service provides options certified for use in food processing zones. These units are designed to withstand daily washdowns and exposure to cleaning agents. By choosing food-safe models, you protect both your workforce and your product integrity.
Mirrors Security and Retail: Loss Prevention and Monitoring
Retail outlets, banks, and public buildings require effective deterrence against theft and vandalism. Observation solutions in these spaces must blend security with aesthetics, supporting both staff safety and customer comfort.
Key Security Features:
- Discreet Design: Compact options integrate seamlessly into modern interiors.
- Anti-Ligature Models: These are essential for public buildings or high-risk areas, reducing the chance of tampering or misuse.
- High-Definition Clarity: Clear, undistorted images support staff in monitoring activities across sales floors and public areas.
Total Locker Service’s security-focused products include anti-vandal and anti-ligature designs, which are suitable for schools, hospitals, and busy retail locations. Options for both ceiling and wall mounting add to their versatility.
Mirrors Selecting the Right Material
Materials impact both durability and suitability for different environments. Understanding the available options helps ensure your investment lasts.
- Acrylic: Lightweight, impact-resistant, and economical, acrylic is ideal for light-duty applications or temporary setups.
- Polycarbonate: Significantly tougher than acrylic, polycarbonate withstands heavier impacts and extreme temperatures. It is a preferred choice for industrial and outdoor use.
- Stainless Steel: The top choice for food and hygiene-critical areas. Stainless steel resists corrosion, chemicals, and high-temperature cleaning processes.
Total Locker Service lists the material type with each product, enabling you to match features with your operational requirements.
Installation: Maximising Effectiveness
Proper installation maximises visibility and security benefits. Before ordering, survey your premises for high-risk zones, blind spots, or complex intersections.
Best Practices for Installation:
- Height: Position units at eye-level or slightly above for optimal field of view.
- Angle: Use adjustable mounts to cover wide areas and eliminate hidden corners.
- Fixing Method: Select between wall, ceiling, or pole mounts based on your available infrastructure.
Total Locker Service supplies comprehensive installation guides and offers support for bespoke setups. Their mounting kits are designed for easy adjustment and secure attachment.
Mirrors Choosing the Right Size and Shape
Observation solutions are available in various sizes and shapes. The optimal choice depends on the area to be monitored and the purpose.
- Convex Models: Provide a panoramic view, ideal for corridors, warehouse aisles, and roadways.
- Dome-Shaped Units: Discreet and effective for monitoring lobbies, reception desks, and public waiting areas.
- Rectangular Options: Useful for tracking long production lines or overseeing multiple workstations simultaneously.
Total Locker Service can assist with sizing calculations, ensuring full coverage without unnecessary overspend.
Mirrors Additional Features and Customisation
Advanced features help tailor solutions to your unique business environment.
- Anti-Fog and Anti-Scratch Coatings: Extend lifespan and reduce maintenance costs.
- Weatherproof Designs: Essential for outdoor use or exposure to fluctuating conditions.
- Coloured Borders or Frames: Improve visibility and reinforce safety messages in industrial settings.
Custom options from Total Locker Service include branded frames and specialist coatings. Discuss your requirements with their team for a perfect fit.
Mirrors Compliance and Regulatory Considerations
Certain industries must comply with strict safety or hygiene regulations. Using the correct product can be the difference between passing or failing an inspection.
- Health and Safety Standards: Industrial and food environments may be inspected for proper visibility aids.
- Anti-Ligature Requirements: Institutions such as hospitals and schools are often legally required to install tamper-resistant models.
- Food Hygiene Compliance: Food processors must use certified equipment that is easy to clean and resists contamination.
Total Locker Service ensures that each item in its range meets relevant UK and European regulations. Documentation is available to assist with audits and inspections.
Budget and Return on Investment
Although price is always a factor, consider the return on investment. Premium products provide longer service life, less maintenance, and enhanced safety.
- Upfront Cost vs. Longevity: Investing in a robust, industry-specific solution reduces replacement frequency and minimises downtime.
- Improved Productivity: Clearer visibility decreases accidents and increases workflow efficiency.
- Lower Insurance Premiums: Improved safety measures may help reduce insurance costs.
Total Locker Service offers a variety of options to suit different budgets. Their experienced team can recommend solutions that deliver long-term value.
Case Study: Warehouse Safety Upgrade
A large distribution centre faced frequent incidents at busy intersections between aisles. After a site survey, the manager installed polycarbonate convex models from Total Locker Service at every junction. The result was a significant reduction in forklift collisions and improved compliance with health and safety regulations. Easy cleaning and durability kept maintenance costs low, further supporting the centre’s bottom line.
Case Study: Food Processing Facility
A regional food processor needed to enhance observation in a wet, high-humidity environment. The company selected stainless steel units with anti-fog coatings, designed and supplied by Total Locker Service. Installed above critical machinery, these units helped supervisors monitor workflows and ensure rapid responses to blockages or hazards. The seamless, easy-clean design satisfied all local food safety audits.
Case Study: Retail Security Improvement
A national retail chain experienced rising stock losses in several branches. Managers chose discreet, anti-vandal observation points from Total Locker Service for each store’s entrance and checkout area. Staff reported improved ability to oversee customer activity, and losses fell by over 30 percent within six months. The anti-ligature design ensured compliance with safety guidelines for public buildings.
Maintenance and Care
Long-term performance depends on proper maintenance. Regularly inspect each unit for signs of damage or clouding. Clean with appropriate solutions based on the material type—avoid abrasive cleaners on acrylic and use stainless steel-safe products where required.
Total Locker Service provides care instructions with every purchase. Their support team can also advise on cleaning products and schedule maintenance if required.
The Total Locker Service Advantage
Choosing Total Locker Service means access to deep expertise, robust products, and responsive customer support. Their portfolio covers a broad spectrum of requirements—from high-visibility industrial tools to discreet anti-ligature options for public and retail spaces.
Each product is tested for reliability and compliance. The company offers installation support, customisation options, and guidance on regulatory matters. This holistic approach ensures your observation solution is effective, compliant, and long-lasting.
Steps to Selecting the Best Observation Tool
- Assess your workspace for blind spots and key risk areas.
- Define the purpose—safety, workflow, security, or hygiene.
- Match the solution to the environment (industrial, food, public, or retail).
- Choose material and shape based on durability and coverage needs.
- Confirm compliance with any industry-specific regulations.
- Plan installation for maximum field of view and staff convenience.
- Set a maintenance schedule to keep visibility clear and equipment in top condition.
Following this process guarantees a solution that meets both your current and future needs.
Conclusion: Invest in Visibility, Reap the Rewards
Enhancing workplace visibility is more than a safety measure; it is an investment in your business’s long-term resilience and reputation. Whether you operate a warehouse, food plant, or retail store, the right observation solution supports better decision-making, safer staff, and stronger performance.
Total Locker Service stands ready to support your selection process with a diverse range, expert advice, and ongoing support. Their commitment to quality and compliance ensures you receive the best product for your operational goals.
Take the first step by surveying your premises, consulting with the experts, and choosing a solution designed for your unique business needs. Improved visibility is always within reach—with the right approach, you can ensure safety, efficiency, and peace of mind for years to come.
Discover more from Blog Total Locker Service
Subscribe to get the latest posts sent to your email.