Optimising Packaging for Locker Number Discs
November 29, 2024
Reduce Production and Installation Time
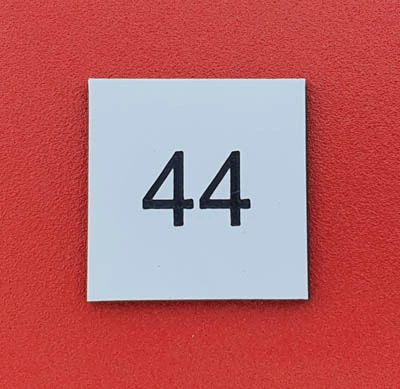
Locker number discs are vital components in the modern locker system. They help identify each locker for easy access, and their efficiency is crucial for both the production and installation phases. Additionally, optimising packaging can further enhance their overall effectiveness.
Optimising their packaging can play a significant role in reducing both production time and installation time. This article will explore strategies to enhance the packaging process of locker number discs. It will offer solutions that lead to more streamlined production. These strategies will result in faster installations.
The Importance of Efficient Packaging
Efficient packaging is not just about reducing the amount of material used. It’s also about improving the entire logistics and handling process. When locker number discs are packaged efficiently, handling time decreases, and the risk of damage during transportation is minimised. Furthermore, well-organised packaging makes the installation process smoother. With reduced preparation and handling times, workers can focus on the task at hand rather than sorting through disorganised packaging.
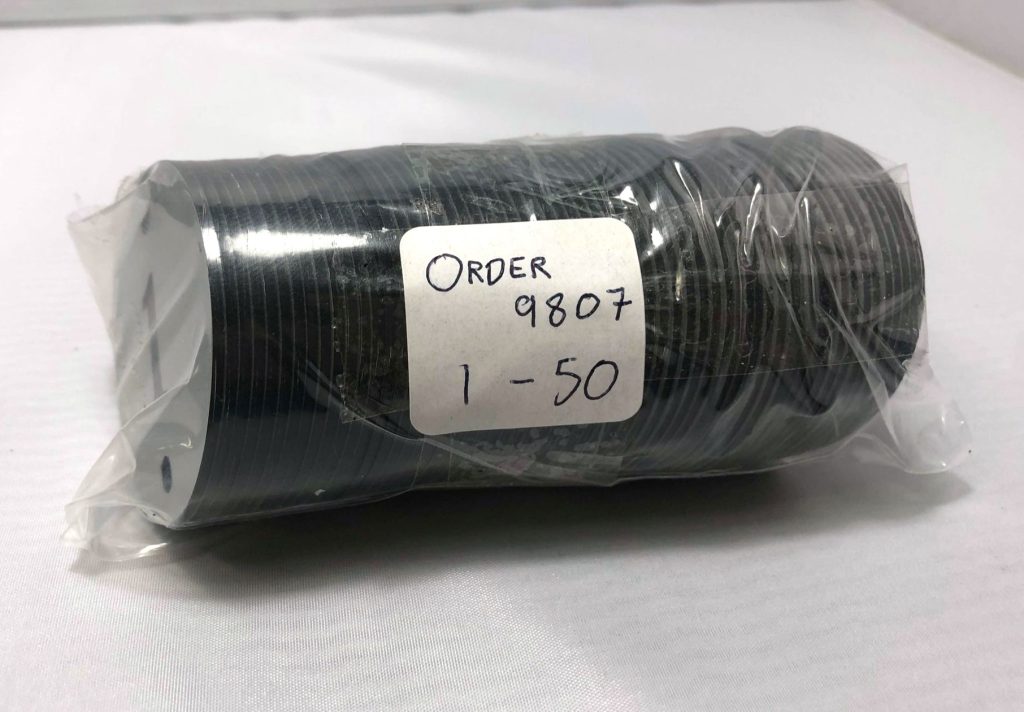
Key Strategies for Optimising Packaging
There are several key strategies to optimise packaging for locker number discs. These range from choosing the right materials to designing compact and functional packaging. Each step plays a role in reducing both production and installation times.
1. Streamlining the Number Disc Design
The design of the locker number discs themselves can contribute to more efficient packaging. By standardising the size and shape of the discs, manufacturers can optimise packaging and storage. A uniform design allows for better stacking and arrangement, making packaging more compact. Furthermore, uniform discs can be arranged in pre-determined patterns, reducing time spent sorting and packing.
2. Using Modular Packaging
Modular packaging is one of the most effective ways to optimise space and reduce time in both production and installation. By using modular packaging, locker number discs can be stored in compact, organised units. These units can then be stacked or arranged efficiently for easy transport. This modular system not only saves space but also allows for easy access during installation. Rather than having to search for specific discs, installers can work directly from pre-packaged units, saving valuable time.
3. Incorporating Pre-labelled Packaging
Pre-labelled packaging significantly reduces the need for time-consuming sorting during installation. Labelling packaging according to locker row numbers helps installers identify the correct number discs easily. They can quickly retrieve them from specific lockers. This reduces the risk of errors and eliminates the need for additional handling. Moreover, pre-labelling helps avoid confusion, ensuring that each locker receives its correct disc quickly and efficiently.
4. Implementing Protective Packaging Materials
While reducing material usage is important, ensuring the discs are protected during transport should remain a priority. Protective packaging materials, such as foam inserts or padded trays, help reduce the likelihood of damage. Production delays are reduced when discs are protected from damage. This protection also decreases the time spent correcting errors during installation. Strong, lightweight materials also contribute to a faster, more efficient packaging process.
5. Maximising Box Efficiency
The boxes used to ship locker number discs should be designed with efficiency in mind. Custom-sized boxes can maximise the space available for discs. They reduce excess room that would otherwise lead to wasted space and disorganisation. Properly sized boxes reduce both the cost of packaging materials and the weight of shipments. This can help improve overall logistics efficiency and reduce transport costs.
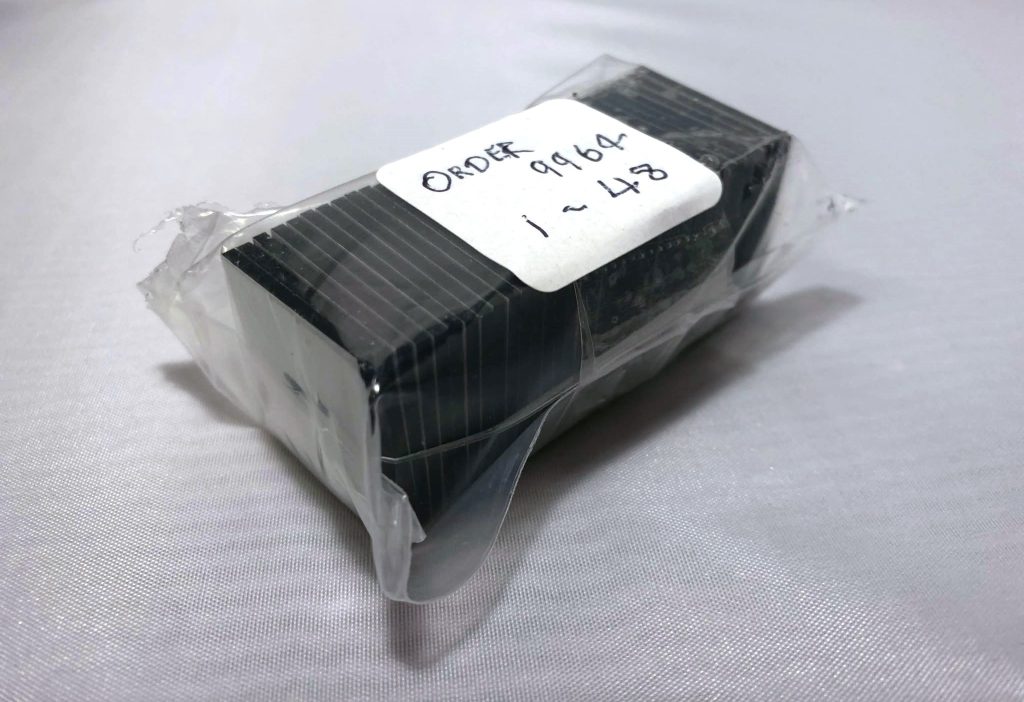
Streamlining Production Time
The packaging process directly impacts production time. If the packaging method is inefficient, it can slow down the entire production line. Manufacturers can reduce the amount of time spent on packing by improving how locker number discs are packaged. This improvement increases their overall production speed.
1. Automation of Packaging Processes
Incorporating automated systems in the packaging process can drastically reduce production time. Automated machinery can quickly sort, pack, and label locker number discs. This reduces the need for manual labour. It also speeds up the process. Automation ensures that the discs are consistently packed and labelled correctly, reducing human error. Additionally, automated systems can adjust the packaging configuration on-the-fly. This allows for easy adaptation based on different disc sizes or packaging requirements.
2. Streamlined Sorting Systems
Integrating a streamlined sorting system into the production line helps keep the packaging process efficient. Rather than manually sorting discs by size or number, automated systems can sort the discs based on predefined criteria. This reduces time spent sorting during packaging and ensures a smoother transition from production to packing. The result is faster turnaround times, with fewer delays between production and shipment.
3. Standardisation of Packaging Components
Standardising packaging components—such as the size of boxes, trays, and labels—reduces time spent adjusting equipment or changing packaging materials. This uniformity simplifies the entire production process, enabling employees to work faster and with fewer interruptions. When packaging is standardised, production lines can maintain a steady rhythm, reducing the risk of bottlenecks and inefficiencies.
Reducing Installation Time
Once the locker number discs have been produced and packaged, the next step is installation. Efficient packaging directly impacts installation time. If packaging is optimised, the entire installation process becomes quicker and more straightforward.
1. Pre-packaging for Easy Access
Packaging the locker number discs in such a way that they are easily accessible during installation can save significant time. There is no need to unpack and organise discs at the installation site. Pre-packaged units can be directly accessed. They can be used as needed. This minimises delays in finding the right discs and eliminates unnecessary sorting during installation.
2. Organising by Locker Groupings
To further streamline installation, packaging can be organised by locker groupings or rows. Each set of discs for a specific locker group can be packaged together. This reduces the time it takes to retrieve and install the discs. Installers can move through the installation process more efficiently by organising packaging to match the lockers’ layout directly.
3. Training for Efficient Handling
Even with optimised packaging, proper training is essential for installation teams. Workers should be familiar with the packaging system and understand how to handle it efficiently. Training teams to quickly access and organise the locker number discs can further reduce installation times. Well-prepared teams are more likely to work quickly and accurately, keeping installation on schedule.
Packaging Innovations for the Future
The packaging of locker number discs is an area that continues to evolve. As technology advances, new packaging solutions are emerging that promise even greater efficiencies. RFID tags embedded in packaging could track locker number discs in real-time. This tracking can happen both during production and installation. These advancements will reduce errors, improve inventory management, and ultimately shorten both production and installation times.
1. Smart Packaging Solutions
Smart packaging solutions involve the integration of technology into packaging materials. For instance, NFC or RFID tags could be embedded in the packaging. They could also be placed in the discs themselves. This allows for real-time tracking and inventory management. This reduces the time spent manually checking and sorting discs during production and installation. Such solutions could improve the accuracy of disc identification. They ensure that each locker receives the correct disc with minimal effort.
2. Eco-friendly Packaging Materials
Sustainability is becoming a priority in packaging design. Eco-friendly packaging materials can reduce the environmental impact of manufacturing and transportation. Recyclable, biodegradable, or reusable materials can help manufacturers reduce waste while maintaining packaging efficiency. These sustainable practices not only support green initiatives but also contribute to cost savings, reducing production time and material costs.
Conclusion
Optimising the packaging of locker number discs offers clear benefits for both the production and installation processes. By streamlining design and using modular and protective packaging, manufacturers can save time. Automating systems and organising packaging for easy access further reduces the time needed for both production and installation. As packaging technologies continue to evolve, the potential for even greater efficiencies will emerge. Ultimately, the goal is to create a packaging system. It should save time. Additionally, it should improve the overall quality and reliability of locker number discs.